Just a year ago, full size plan digitization projects were reserved for the front-runner companies, that had the vision and will to make digital plants a competitive edge for them. Nowadays, however, COVID-19 has forced production plant owners to take measures to ensure critical operations, even when support staff and external contractors cannot visit the site.
eSite has worked long days during the past months to help plant owners and industrial service providers to digitize plants and make it possible to work at them remotely. For instance, last week we digitized three full size power plants and the week before another three industrial facilities. And most of them were even in different countries!
Our Solution
To ensure operational excellence and safety, these days when travelling to the sites is not the preferred option, eSiteview is a solution to digitize a full power plant (or other industrial plant) in just a day. This way plant owners, operators, maintenance staff, contractors and equipment suppliers can visit the plant remotely. They will get a good understanding on what the site conditions are, take measurements, share information and communicate with local operators efficiently. Critical stakeholders get an accurate understanding of the plant. Thus, they can perform their work effectively, whether it is related to plant operations, plant maintenance or CAPEX projects.
For a broader explanation on our new re-engineered eSiteview solution, you can read our previous article.
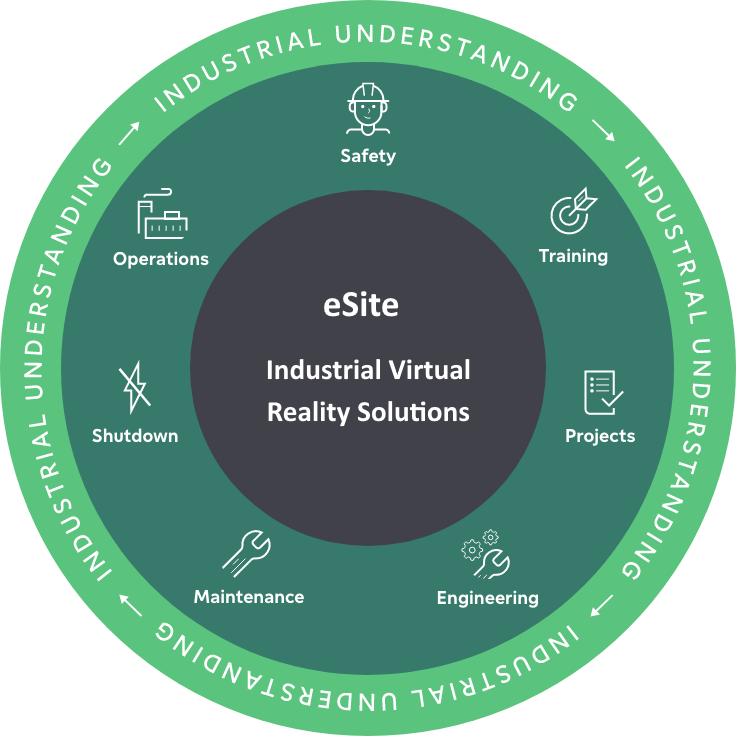
So why have we been asked to digitize so many power plants?
Power plants are critical assets in the infrastructure, they need to be operational even in the most unpredictable times. That is why they have been the first to act in preparing for the future. Here are three reasons why our customers have urgently digitized their power plants during the past months:
1. To ensure critical projects don’t get delayed or run out of budget.
Time is money and each day that the plant is not in operation can represent huge costs. So, when COVID19 hit, several plants struggle to keep their critical projects moving. Contractors, equipment suppliers and other specialists were not able to physically visit the plant as they traditionally do.
With eSiteview solution, our customers were – and are – happy to have all the plant available and accessible online and have the possibility to permit selected stakeholders to visit it remotely. They said that the digitizing time was fast and inexpensive. This has helped critical projects to keep moving on time and without additional costs.
2. To keep plants operating by improving communication while avoiding personal contact.
In previous times, external maintenance contractors and support staff visited the plant often. They discuss operational and maintenance issues, take pictures of the equipment and take measurements for maintenance work planning. During the past months, this has not been possible to the same extent.
With eSiteview solution, the plant staff and external service providers can accurately point at places, equipment and structures at the plant. They can have web meetings, where all parties take together virtual visits to the plant and solve problems. People working remotely can also make accurate requests for field information, pinpointing the exact equipment from which information or pictures are needed. They can then, send this request to field operators, whom can, directly from their mobile phone, take and attach pictures. This supports remote work without the risk of disturbing production.
3. To mitigate the risks during the second wave and to keep competitive in the new normal.
During the first wave of COVID19, several plants had to shut down or take other actions to avoid loosing operational resources. These companies suffered strongly from these mitigation actions. Now that plant owners are aware that a second wave is on its way, they are preparing better for it.
With eSiteview solution a power plant (or other industrial facility) can be completely digitally mapped in as little as one day. Our customers have requested us to digitize even small fleets of power plants. By letting our eSite team visit the plant once, it will be possible for hundreds or thousands of people visit the plant later without any risk of disturbance in the operation and maintenance activities.
Some customers have even seen a silver lining in this dark cloud. People at the plant and around it have been forced to change their way of working and avoid unnecessary travelling to the site. They have also become more empathetic by providing remote support to their colleagues at the site. This receptiveness will help companies adapt better to the new normal and will give them a competitive edge in the future.
So, what are your benefits as a plant owner to have eSiteview solution?
To sum up, there are not only three reasons why it is valuable to have a power plant digitized in one day. There are dozens of reasons why you will benefit from digitizing your plant. To put it in a simple way, you will:
– Increase productivity
– Reduce occupational risks -> safer workplace
– Reduce maintenance costs
– Reduce operative costs
– Execute better projects
– Improve the value you deliver to your customer
– Save time
– Avoid mistakes and misunderstandings
– Improve communication between all stakeholders
– Improve staff motivation
– Be better prepared for future times of uncertainty
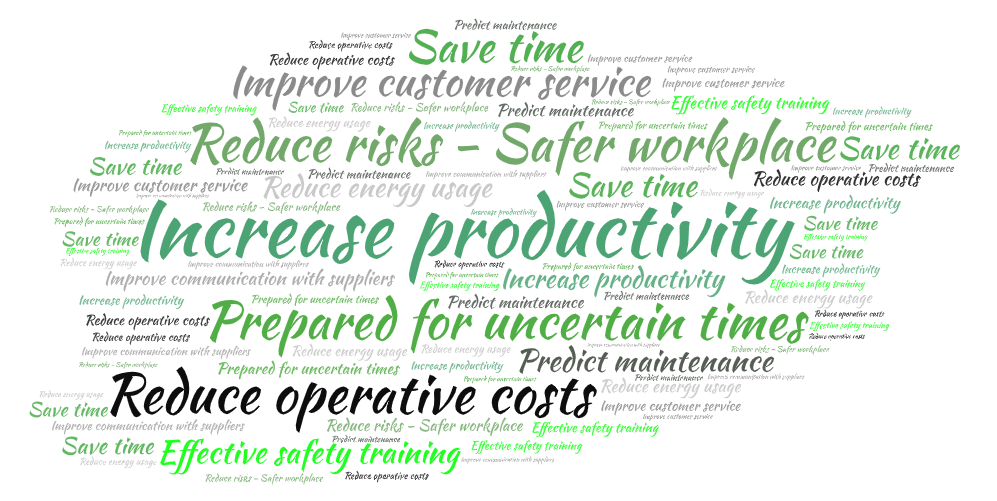
If you are a plant owner or a decision maker related to an operating plant, why hesitate? Contact us and our partners to digitize your plant and verify the benefits for yourself. Contact us for a quotation or ask for a demonstration. We are now available for all industry sectors and all around Finland. We also perform work in countries around the world.
The next article titled “How can construction sites all around Finland be visited remotely?” will be published on 28.9.2020. Stay tuned and like our LinkedIn posts eSite