Whenever a production facility stops its normal operations, it also stops generating revenues and starts increasing expenses. That’s why, planned outages are a fundamental part of any plant’s operational excellence. To avoid unnecessary losses, successful outages require months of preparation and planning before the actual downtime takes place.

Plant staff and external contractors usually need to visit the plant several times before the actual outage takes place
There are three indicators during the outage process: the pre-outage indicators, the outage execution indicators, and the post-outage evaluation. During the first phase, the organization must identify the activities that require attention during the outage and the metrics that will be used in the post-outage evaluation. Only after this step is completed, the planning can start.
During the planning phase, it has been common that plant staff and external contractors visit the site several times. This is because they need to plan carefully different aspects of the outage and work to be performed: amount of resources needed, working conditions, what assets need to be overhauled and their locations, scheduling the work sequence, material and tools required, safety requirements, etc. For example, one of our customers mentioned that if some outage work requires interaction with cable trays/routes, this often requires several visits to the site to check details and take pictures, which you need for good preparation. This translates into unnecessary travel costs, errors in engineering and slow planning process, and you often don’t get everything right the first time around.
“This traditional way is not anymore feasible, we need to find a way to plan our outages without visiting the site physically”
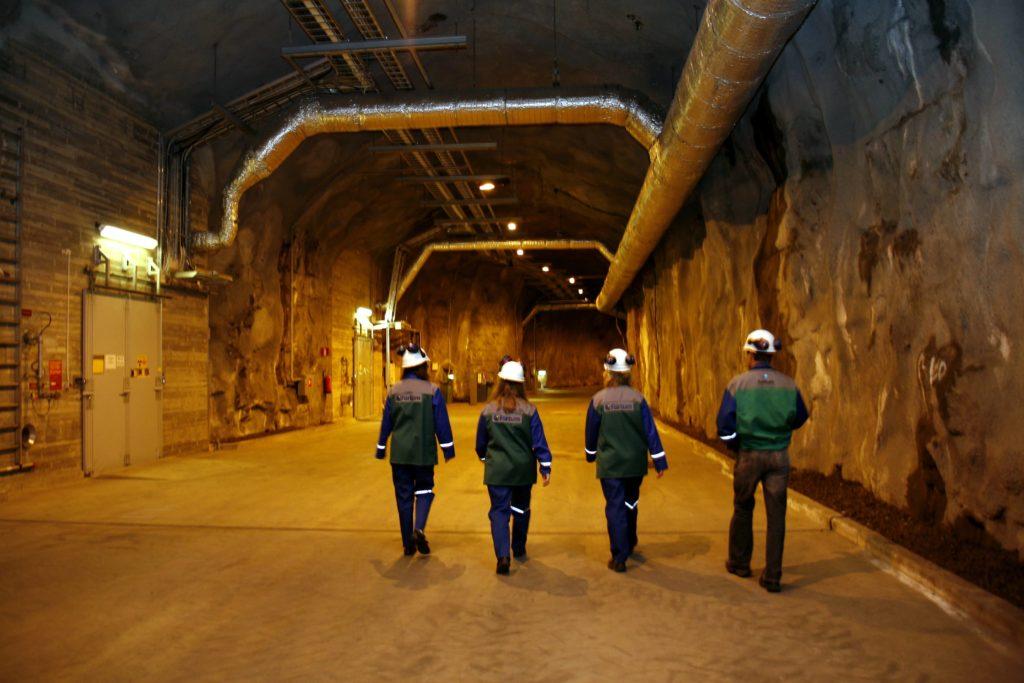
Times have changed however, and at the moment is not possible to travel to the plant facilities as freely as before. This has caused a negative impact on the industrial production worldwide. According to the Eurostat, most industries in the EU dropped their production to levels only seen in the 1990s crisis. And this downturn is global, major industrial companies in the US have also shut down. Therefore, it is crucial to find an immediate solution as current times are not expected to change anytime soon.
“For companies vulnerable to a viral outbreak within their ranks, this would be a critical time to explore a proactive deployment of automation technologies to decrease worker density throughout their operations” Pwc
A successful outage also means zero accidents, therefore there are some locations on the site, where visiting is not even advisable because of safety reasons. E.g., hazardous areas with radiation in nuclear industries, heat in steel industries, magnetic fields in power generation industries, hazardous fumes in chemical industries, etc. In these cases, digitization of the site is even more urgent. And the costs of accidents are pricey. In Finland, €2 – €2.5 billion a year is lost due to accidents at work. According to the National Institute of Occupational Health, one accident at work costs the employer an average of €6000.
eSiteview is a virtual duplicate of your site where you can plan maintenance tasks accurately, visualize production data, or even measure if it is safe to perform your tasks.
To make it possible to plan for outages without visiting the site and to ensure zero accidents while doing this, eSite has come up with a solution that digitizes a plant (or any other industrial site) in just a day. This way, plant owners, operators, maintenance staff, external contractors and equipment suppliers can plan their work for the outages remotely. eSiteview is a virtual duplicate of your site where you can mark maintenance tasks accurately, visualize production data, or even measure if it is safe to perform your tasks.
Plant staff and contractors get an instant understanding on what the working conditions at site are. This way they can take measurements, share information and communicate with local operators efficiently and all this work is done remotely. The only time when the field workers, contractors and maintenance personnel need to go to the physical location is when the actual outage takes place. And even then, they do not need to be all on site at the same time, as some work can be monitored remotely.
The value from the use of eSiteview can be seen already during the first month, and the return on investment is immediate. For example, one of our customers, with a large production site, calculated that with eSiteview they save money each month, already if three contractor visits can be cut, and they can do the inspections remotely instead. And for smaller sites the payback is already achieved by reducing contractor visits by one.
Finally, we can say that it is a fact that with eSiteview you can have successful outages with zero prior visits to the site.
Are you planning your next outage and thinking how to do it more efficiently? Contact us immediately and we can arrange a demonstration how eSiteview will help you in your work.
Keep posted
If you want to stay tuned on how we progress on our road-map; with new use cases, reference projects, and new partners, please subscribe as follower to our LinkedIn account and visit our web page.
This has been an article in our article series “capture your site, control your world”. Our next article will be published on 25.11.2020. Stay tuned and give your feedback in our LinkedIn pages: eSite